We respond quickly to injection molding of various materials and shapes.
We manufacture molds using aluminum material (A7075S) with excellent machinability. Furthermore, we will respond quickly to the needs of the R&D department by utilizing the experience that Daytech has accumulated while working on the small lot molding.
General | Our technology | |
Usage | Prototyping(Test pieces before mass production) | Prototyping and reliability test at development phase. Small lot mass production. |
Material | Steel, NAC80, etc. | A7075S, depending on the usage. |
Possible number of shots | 500-1500 | 10,000 shots, depending on the shape. |
Supported plastic materials | Mainly general-purpose plastic | Aslo handle engineering plastics. |
Supported plastic shape | Simple shape. | Complex shapes are available |
Supported surface treatment | Limited. | Wide variety of options. |
We manufacture at high speed by directly processing the mold (A7075S) with less restrictions. A7075S, which is also known as extra super duralumin, is the strongest material among aluminum alloys and is used in aircraft as well.
We handle fine shapes which are difficult to achieve by cutting and helical shapes with ATC (Automatic Tool Changer) and die sinking electrical discharge processing machine with an additional axis. We divide and produce the electrodes in-house aiming to automate the mold manufacturing by ATC.
Please let us know if you have any request.
Achievements which have been made
We respond to the following inquiries by our “molds”.
Request for molding under some certain conditions with the materials provided.
Require the mold to be manufactured using engineering plastic material within short delivery periods
Request for a molding sample with a complex shape like a connector
Cutting processing has been carried out because the number of lots is small, can it be replaced with injection molding?
Mass production mold and prototype mold
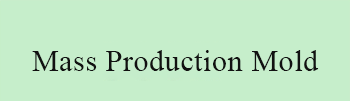
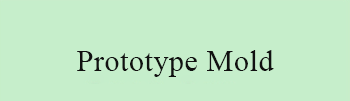
Daytech takes the prototype mold which is especially for the small lot mass production as the “mass production and small lot mold” and has accumulated our original know-how in the molding manufacture corresponding to “1 to 10,000 pieces”, which is different from the generally called “prototype molds”.
The quantity is large for prototyping
Shapes and resin materials that are difficult for cutting processing
The number of lots is too small for the products to transfer to mass production
In such cases, the cost is reduced by about half compared to the case where resin cutting is performed each time.
Unique technology for small lot mass production molding
The product accuracy (from ± 0.02 to ± 0.05) of the prototype mold manufactured by Daytech is equal to or higher than that of mass production mold. Since the aluminum material used for molding is the type of aluminum for molds (class 75), the hardness and machinability of aluminum are significantly different from those of general aluminum.
We are able to realize the precise and complex shapes as we have excellent techniques for special processing such as die sinking electrical discharge machining and small hole electrical discharge machining.
Cost reduction can be realized by utilizing A7075S aluminum plate for mold-based cabinet and the core part
Mass production can be handled effectively and PPSG (super engineering plastic) can be molded without any problem.
Cutting and discharge time can be shortened by adopting the method of placing piece
The shape changes will also be handled flexibly
The compact mold with complex shapes can also be achieved
The construction period is shortened and the cost is lowered as only the essential molds are made
Reduction of material cost and the saving of storage space
Suitable for small lot production
The prototype mold even has a durability of 10,000 shots. The material A7075S for molds is used in the up-to-date machine tools such as high-speed machining center and linear electrical discharge (die sinking electrical discharge, wire cut electrical discharge) machines. We have been challenging all issues relating to delivery time, quality and cost.